Grasping the Art of Welding: Just How to Prevent Undercut Welding Issues for Flawless Manufacture Results
Performance and precision are vital on the planet of welding, where even the least imperfection can jeopardize the architectural integrity of a produced item. One common difficulty that welders face is damaging, a defect that can lead and damage a weld joint to costly rework. By comprehending the origin of undercut welding and carrying out effective techniques to stop it, welders can boost their craft to new levels of quality (Preventing weld undercut). In the search of remarkable fabrication results, understanding the art of welding to stay clear of undercut problems is not simply an ability however a need for those pursuing excellence in their job.
Understanding Undercut Welding
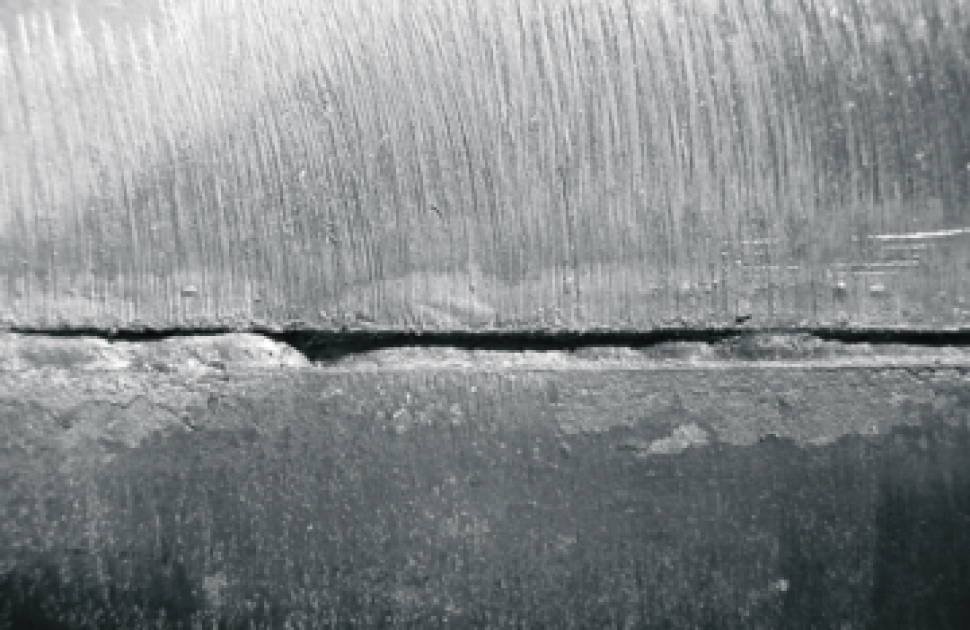
To avoid undercut welding, welders ought to make certain proper welding criteria, such as adjusting the existing, voltage, travel rate, and keeping the proper electrode angle. Additionally, making use of the suitable welding strategy for the particular joint setup is important. Utilizing weaving activities or backstepping techniques can assist ensure proper weld steel deposition and lower the likelihood of undercut formation. Normal inspection of welds during and after the welding process is additionally crucial to catch any type of undercut very early and make required modifications to avoid further problems. Preventing weld undercut. By recognizing the reasons of undercut welding and implementing preventive procedures, welders can attain high-quality, structurally sound welds.
Sources Of Undercut in Welding
Understanding the aspects that add to undercut in welding is crucial for welders to produce high-grade, structurally sound welds. Insufficient welding wrong or current welding speed can additionally add to undercut. Comprehending these reasons and implementing appropriate welding strategies can help avoid damaging concerns, ensuring durable and strong welds.
Methods to Protect Against Undercutting

To reduce the danger of undercutting in welding, welders can employ strategic welding techniques intended at boosting the high quality and stability of the weld joints. Additionally, using the correct welding strategy for the details joint arrangement, such as weave or stringer beads, can contribute to reducing damaging.
In addition, appropriate joint preparation, including making certain tidy base materials devoid of contaminants and making use of the proper welding consumables, is vital in stopping undercut problems. Using back-step welding strategies and managing the weld bead account can likewise help disperse heat evenly and decrease the danger of undercut. Regular inspection of the weld joint throughout and after welding, in addition to implementing top quality assurance measures, can assist in addressing and finding undercutting concerns quickly. By implementing these methods vigilantly, welders can achieve perfect fabrication results with marginal undercut problems.
Significance of Correct Welding Parameters
Selecting and maintaining appropriate welding specifications is crucial for achieving successful welds with marginal defects. Welding specifications you could try here refer to variables such as voltage, existing, travel speed, electrode angle, and shielding gas circulation rate that directly affect the welding process. These specifications have to be carefully changed based on the sort of product being bonded, its density, and the welding strategy used.
Correct welding criteria ensure the best amount of heat is put on melt the base metals and filler material uniformly. If the parameters are set expensive, it can result in excessive heat input, causing burn-through, distortion, or spatter. On the other hand, if the parameters are also reduced, insufficient combination, lack of penetration, or undercutting might take place.
Top Quality Guarantee in Welding Workflow

Conclusion
In verdict, grasping the art of welding needs an extensive understanding of undercut welding, its causes, and strategies to avoid it. By guaranteeing correct welding criteria and executing quality control methods, flawless construction results can be attained. It is vital for welders to regularly pursue excellence in their welding procedures to prevent undercut issues and create top quality welds.
Undercut welding, an usual flaw in welding processes, takes place when the weld metal does not correctly load the groove and leaves a groove or anxiety along the bonded joint.To avoid undercut welding, welders need to make sure proper welding specifications, such as readjusting the current, voltage, traveling speed, and preserving the proper electrode angle. Insufficient welding inaccurate or existing welding speed can likewise add to undercut.To reduce the threat of undercutting in welding, welders can utilize critical welding techniques aimed at boosting the quality and stability of the weld joints.In final thought, understanding the art of welding requires a complete understanding of undercut welding, its reasons, and techniques to avoid it.